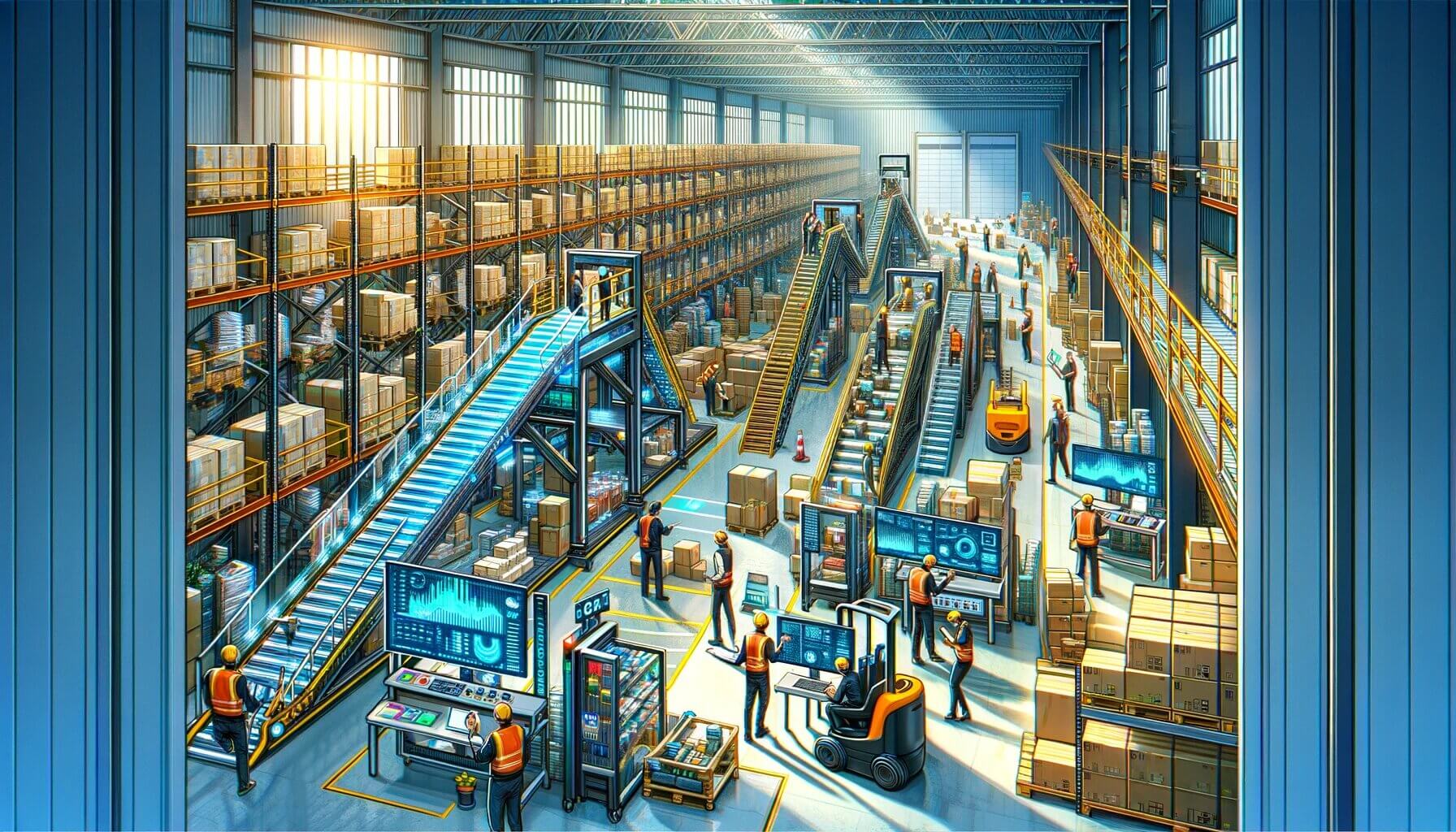
As peak season approaches, logistics take center stage for businesses seeking to benefit from this high-demand period. Effective preparation not only ensures operational success but also improves customer happiness and increases profitability. This detailed guide will support and motivate you through the key processes and methods for optimizing your logistics and preparing your business to handle peak season demands.
Understanding Peak Season in Logistics
What is Peak Season?
In the world of logistics, “peak season” refers to certain periods of the year when company demand significantly increases. The industry, consumer behavior, and market developments all affect this time frame. Many people find that it falls around important shopping occasions and holidays, such as Cyber Monday, Black Friday, and the commercial Christmas season. Other industries may peak at other seasons, such as summer for beverage firms or the back-to-school season for educational providers. Holiday shopping seasons and harvest seasons for farmers are two common examples. To handle the increasing volume of goods, control delivery schedules, and preserve customer satisfaction during these periods, effective logistics are essential.
The Importance of Peak Season Preparation
Peak season demand can put a lot of stress on your logistics operations if not managed effectively. Preparation helps to reduce risks such as stockouts, delayed shipments, and customer unhappiness. Effective management at this time is critical for preserving service quality, reducing costs, and increasing overall efficiency.
Identifying Your Peak Season
Each business’s peak season will differ depending on its industry and consumer base. For instance:
- Retail businesses may have increased sales around Black Friday and Christmas.
- E-commerce stores could peak on Cyber Monday and throughout holiday sale periods.
To make successful preparations, identify your peak periods by analyzing:
- Historical Sales Data: Review past sales to pinpoint high-demand periods.
- Market Trends: Stay updated on industry trends that might affect consumer behavior.
- Competitor Analysis: Understand when your competitors experience high demand, as it can indirectly influence your peak periods.
Identifying your exact peak times aids in planning and resource allocation, ensuring that your company is adequately prepared for the rise in demand.
Planning for Peak Season
Forecasting Demand
Accurate demand forecasting is required to prepare for an influx of orders during peak seasons. Use historical data, client purchase trends, and predictive analytics techniques to properly forecast future demand. This aids in synchronizing your inventory levels, workforce, and delivery capability to meet expected requests without overburdening resources.
Inventory Management Strategies
Proper inventory management is essential to avoid overstocking and running out of supplies. Implement the following tactics for good inventory management:
- Safety Stock: Keep additional stock to cover unexpected demand surges.
- Just-in-Time Inventory: Align your inventory replenishment with demand to reduce holding costs and increase inventory turnover.
- Automated Replenishment: Employ automated systems to reorder stock based on real-time sales, reducing the likelihood of human error.
Strengthening Warehousing Operations
The effectiveness of your storage operations has a direct impact on your ability to meet growing demand. Consider the following enhancements:
- Optimized Layout: Reorganize your warehouse to streamline operations and reduce handling time.
- Smart Storage Solutions: Utilize vertical storage and automated retrieval systems to maximize space.
- Advanced Warehouse Management Systems (WMS): Implement WMS to improve inventory accuracy and order processing speed.
- Efficient Picking Processes: Adopt multi-order picking techniques to speed up operations.
- Labor Management: Deploy your workforce strategically to meet operational demands without unnecessary labor costs.
Leveraging Technology in Logistics
Automation and Robotics
In today’s tech-driven logistics market, organizations looking to maximize logistics operations must rely on automation and robotics. These technologies are especially successful in:
- Automated Sorting Systems: They speed up the sorting process and reduce errors in order fulfillment.
- Robotic Picking Systems: These can enhance picking efficiency and reduce the physical strain on workers.
Advanced Tracking and Reporting Systems
- GPS Tracking: Offers real-time location tracking for shipments.
- Performance Dashboards: Provides insights into operations, helping to quickly identify and rectify inefficiencies.
- Customer Portal Access: Allows customers to track their orders, enhancing the customer experience and reducing service calls.
Optimizing Transportation
Efficient Route Planning
Sophisticated route planning software can optimize delivery routes by taking into consideration factors like traffic patterns, delivery windows, and vehicle capacity. This not only shortens delivery times but also saves fuel and wear on trucks.
Collaborative Logistics
Partnering with other businesses can spread out the cost and complexity of logistics operations. Consider engaging in collaborative logistics practices such as:
- Shared Warehousing: Reduce costs by sharing storage space with other businesses.
- Joint Distribution Agreements: Pool resources for distribution and benefit from reduced costs and expanded network reach.
- Carrier Collaboration: Working closely with your shipping companies can result in more consistent service during peak periods. Negotiate terms and conditions that meet peak demand and ensure carriers are ready for more shipments.
Staffing and Training
Scaling Workforce
To properly handle peak season requirements, adjust your workforce in reaction to expected demand. Employ temporary workers to support your regular staff as needed, but make sure that all workers are adequately trained to satisfy your service requirements.
Comprehensive Training Programs
- Customer Service Excellence: Prepare your team to handle high volumes of customer interactions professionally.
- Efficiency and Safety Training: Ensure all employees understand how to work efficiently and safely, particularly when under the pressure of increased demand.
Continuous Improvement
Post-Peak Season Review
After the peak season, undertake an in-depth analysis of what went well and what could be improved. Gather insights from data analytics, consumer feedback, and staff reviews to help you plan for the future.
Implementing Improvements
Use the information acquired to fine-tune your logistics plan. Continuous improvement enables your company to respond to market and consumer trends, ensuring preparation for future peak seasons.
Conclusion
It takes careful planning, strong technological integration, and smart operations management to get ready for peak season. Through foresight, process streamlining, and the application of advanced technologies, your company may surpass rivals and effectively manage the demands of peak season. Recall that effective peak season logistics management creates the conditions for long-term customer happiness and increased profitability in addition to helping businesses survive the demand spike.
From accurate demand forecasting to leveraging cutting-edge technology and collaborative logistics practices, Wahyd Logistics is committed to empowering businesses like yours to thrive in high-demand seasons. With our expertise and innovative solutions, you can confidently navigate peak-season challenges and capitalize on growth opportunities.