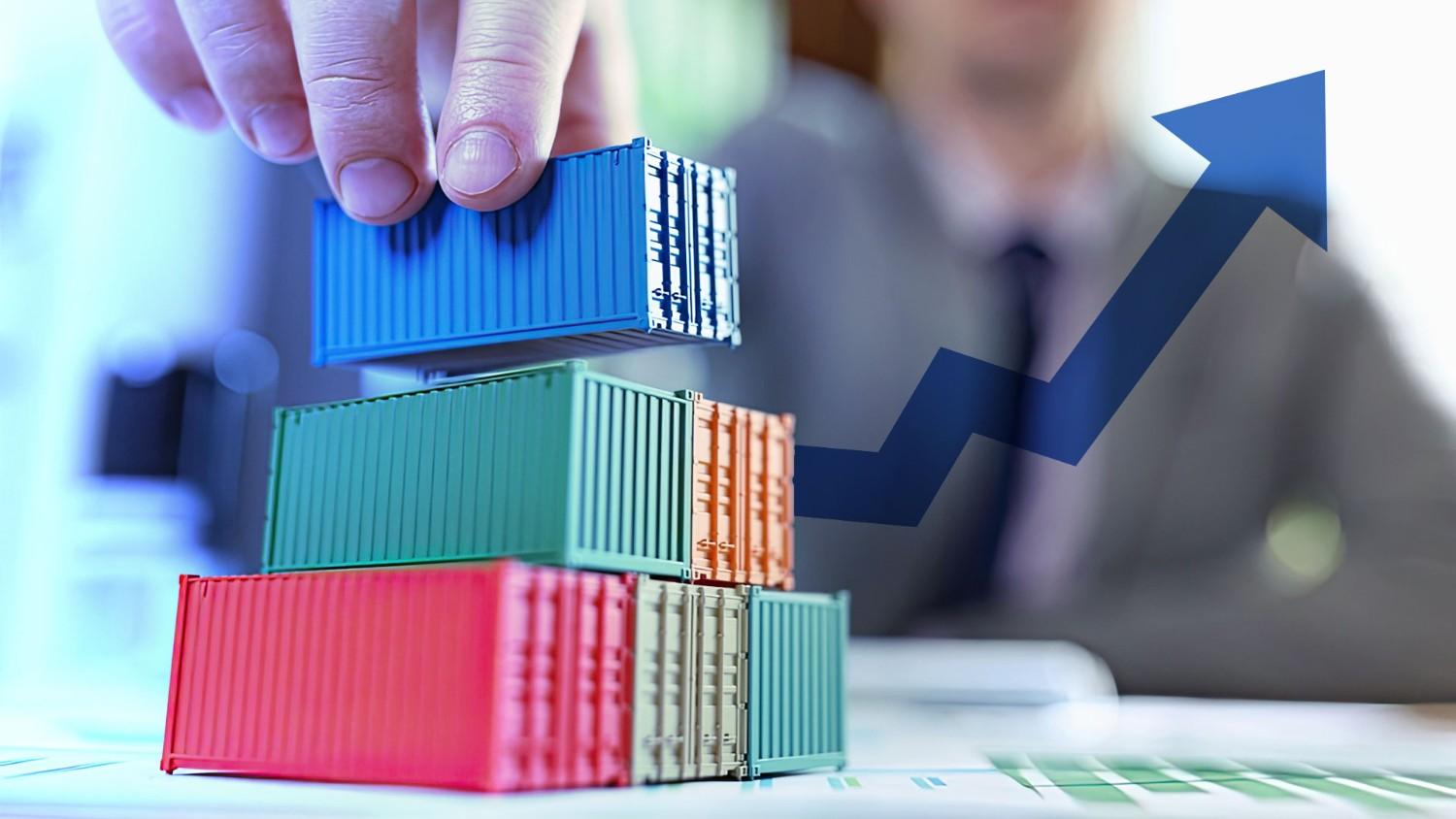
Manual logistics inefficiencies in freight management drive up costs, slow operations, and amplify environmental impacts, underscoring an urgent need for streamlined, tech-driven solutions.
The global demand for goods and services is growing more than ever, and companies are under pressure to move goods faster and more efficiently. However, manual logistics inefficiencies hamper this growth, creating freight backlogs and operational bottlenecks, that lead to significant cost overruns and delays.
In this blog, we will explore how manual processes in logistics create bottlenecks, the impacts of these inefficiencies on freight growth, and the potential solutions that can address these issues.
Understanding Manual Logistics Inefficiencies
Manual logistics inefficiencies refer to the bottlenecks and delays created by outdated, human-reliant processes within logistics operations. Tasks such as data entry, scheduling, inventory management, and freight documentation are still handled manually for most logistics operations. While these processes were once standard practice, they are now proving insufficient to meet the needs of a continuously evolving logistics landscape.
Common Causes of Manual Logistics Inefficiencies
Several key factors contribute to manual inefficiencies in logistics:
- Human error: Manual processes are susceptible to errors, from incorrect data entry to communication breakdowns, leading to delays and increased costs.
- Time-Consuming Paperwork: Freight logistics often involve a wide variety of paperwork, including bills of lading, customs documentation, and scheduling sheets. Handling these manually slow down processes.
- Lack of Real-Time Data: Without digital tracking and data sharing, logistics teams have limited visibility over shipments, making it challenging to manage schedules, route optimization, and unexpected disruptions.
- Dependency on Physical Infrastructure: Manual logistics rely on in-office teams and infrastructure, which limits the flexibility to manage operations remotely or scale up efficiently during peak seasons.
These inefficiencies:
- Slow down logistics operations.
- Lead to increased labor costs.
- Limit the industry’s ability to meet growing freight demands.
Impact of Manual Logistics Inefficiencies
Manual logistics inefficiencies can be a significant contributor to freight backlogs and inefficiencies. When companies cannot move goods as quickly as required, they face several consequences:
- Delays in Freight Movement: Freight bottlenecks occur when logistics processes can’t keep up with the volume. This causes costly delays as shipments sit idle awaiting processing.
- Increased Storage Costs: Freight stuck in warehouses or distribution centers increases storage costs; a compounding burden over time.
- Customer Dissatisfaction: Late deliveries and missed deadlines due to backlogs frustrate customers, leading to lost business.
- Operational Bottlenecks: Manual logistics often create bottlenecks in customs processing, dispatching, and loading, slowing down the supply chain.
Once companies identify and understand the root causes of these inefficiencies, they can start making strategic changes to improve performance and drive freight growth.
How Manual Logistics Inefficiencies Slow Freight Growth
In logistics, manual processes create significant bottlenecks that slow down freight growth and disrupt the efficiency of the entire supply chain. Let’s look at key areas where these issues impact operations:
Shipment Scheduling and Tracking
Manual scheduling is time-intensive and prone to human error, causing delays that ripple throughout the supply chain. Without automated tracking, timely updates on shipment status are difficult to achieve, leading to gaps in communication and missed delivery windows. This inefficient process contributes to backlogs and idle resources, increasing costs for shippers and restricting logistics scalability.
The High Cost of Manual Operations
Manual logistics demands considerable manpower. Brokers juggle endless paperwork and phone calls, while inefficiencies in handling orders and tracking lead to operational slowdowns. The use of manual processes results in empty miles (trucks running without loads), higher emissions, and mounting costs. These issues also exacerbate ESG concerns, placing additional strain on the industry to find sustainable solutions.
Documentation and Compliance
Handling regulatory paperwork manually leads to frequent errors, delays, and breaches in compliance. At customs, misplaced or incomplete documentation can halt shipments, creating bottlenecks that slow freight flow and escalate operational expenses. These inefficiencies increase the time and cost burden on logistics providers, which ultimately trickles down to clients.
Inventory Management Gaps
Without automated systems, inventory management relies on manual updates, often resulting in mismatches between inventory data and actual stock levels. Such inefficiencies lead to stock imbalances, delays, and order fulfillment issues. This lack of precise, real-time inventory management intensifies backlogs and heightens the risk of missed delivery windows, impacting client satisfaction and overall supply chain performance.
The Costs of Manual Logistics Inefficiencies
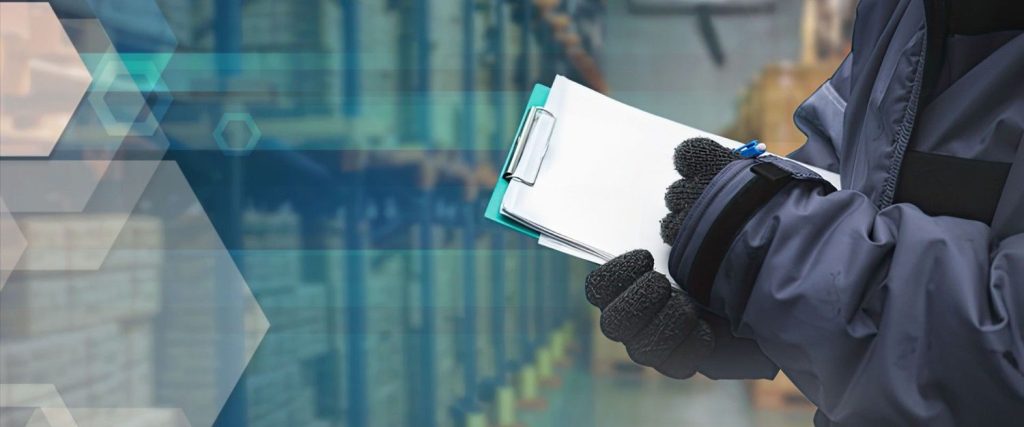
In the logistics sector, manual inefficiencies don’t just slow down processes—they drive up costs and strain resources. Here’s a closer look at how these inefficiencies impact the bottom line:
Labor-Intensive Processes and Rising Costs
Manual logistics relies heavily on manpower, with brokers, drivers, and warehouse staff managing a multitude of tasks by hand. As a result, labor costs skyrocket, especially during peak seasons, limiting scalability and putting pressure on the firm’s ability to expand. This over-reliance on labor drains resources that could be redirected to growth and innovation.
Escalating Storage Costs and Limited Space
Freight delays due to manual inefficiencies often mean prolonged storage times. Goods pile up in warehouses, consuming valuable space and increasing storage costs. As inventory sits idle, companies are forced to expand their storage areas, which drives operational costs even higher.
Expensive Delays and Missed Deadlines
Timing is everything in logistics. Manual scheduling, tracking, and documentation errors frequently lead to delays, impacting both delivery timelines and customer satisfaction. Missed deadlines strain working capital and erode client trust, as customers expect reliable, timely deliveries.
Revenue Loss and Customer Dissatisfaction
Repeated delays and errors not only damage client relationships but also impact revenue over the long term. Dissatisfied clients are likely to seek alternative providers, stalling growth and harming the company’s reputation.
Fines and Regulatory Strains
Errors in manual documentation increase the risk of non-compliance fines. These penalties eat into profits and can damage relationships with regulatory bodies, leading to operational disruptions that further escalate costs.
How to Overcome Manual Logistics Inefficiencies
To overcome costly manual inefficiencies, it’s essential to switch to digital tools and automation. Automating logistics processes helps reduce freight backlogs and speeds up delivery. Here are some effective steps:
Automate Repetitive Tasks
First, automating repetitive tasks like data entry and documentation can eliminate human error. Automation cuts labor costs and allows teams to focus on higher-value work.
Use Real-Time Tracking Systems
Next, digital tracking systems, like those from Wahyd Logistics, let managers monitor shipments in real time. This shows the exact location and status, helping avoid delays and making decisions easier.
Implement Integrated Inventory Management
Integrated inventory software keeps track of stock levels automatically. It can reorder items when needed and organize warehouse space better. This prevents stockouts or overstocking, making freight operations more efficient.
Adopt Digital Documentation for Compliance
Lastly, digital documentation tools simplify compliance. They create, store, and share critical documents without errors. By digitizing these tasks, companies avoid costly compliance mistakes.
The Future of Freight Without Manual Inefficiencies
With new technology, manual logistics inefficiencies are becoming a thing of the past. Companies using modern solutions, like Wahyd’s AI-powered platform, gain a clear advantage in freight growth. Those slow to adapt will struggle to keep up.
Wahyd’s platform is built on cutting-edge AI. It automates every part of the process—from scheduling to tracking—eliminating manual tasks and reducing costs. By using Wahyd, companies experience:
- Scalability: Wahyd’s AI can handle massive freight volumes without adding extra labor costs. This makes growth seamless and cost-effective.
- Efficiency: Wahyd’s automation reduces errors and speeds up logistics. Real-time tracking meets customer needs and avoids backlogs.
- Cost Savings: By lowering labor and storage expenses, Wahyd helps companies save significantly, which can fund further growth.
- Enhanced Customer Satisfaction: Wahyd enables faster, more reliable deliveries. This builds customer loyalty and trust, positioning companies as dependable logistics partners.
Conclusion
Manual logistics inefficiencies hold freight growth back and create costly delays across the supply chain. Recognizing challenges in inventory, scheduling, and documentation is only the first step. Wahyd offers a clear path to overcoming these issues.
With Wahyd’s AI-powered automation, companies can address backlogs, improve service quality, cut costs, and grow. In today’s market, digital transformation is no longer optional. Those who embrace Wahyd’s solution will lead the way in building a faster, more scalable, and customer-friendly logistics industry.